Polyplex 225 molds casting
For the production of flexible molds in casting.
100% solids 100% elongation for making molds by casting
Production of flexible casting molds Polyplex 225 – for the production of flexible casting molds – a thick liquid made of two-component hydrophobic elastomeric polyurethane, flexible and hard, wear-resistant, 100% solids, which polymerizes from a reaction between the base and the hardener. Unlimited thickness and powerful, for making molds for cold casting models. Plaster, epoxy, concrete, acrylic solutions, etc. can be poured into the mold.
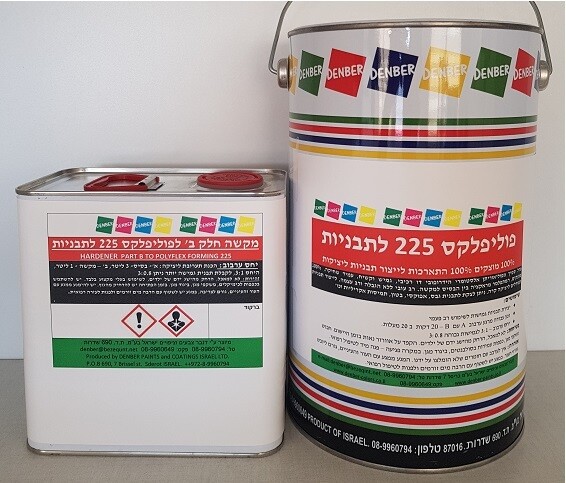
Polyplex 225 molds casting. www.denber-paints.co.il
POLYFLEX FORMING 225 100% SOLIDS, TWO COMPONENT FLEXIBLE FOR INDUSTRIAL STRONG FORMING
For the production of extremely flexible and strong molds for casting, resistant to wear with a unique molecular structure, resistant to wear and mechanical blows and suitable for regular multiple use.
Characteristics:
- Flexible extends at least 100% .
- A perfect seal from water, repels moisture and prevents penetration.
- Resistant to mechanical blows.
- Abrasion resistant.
- Can be applied in one casting without thickness limitation.
- Resistant to thinners and chemicals.
- Excellent adhesion to the infrastructure.
- Easy to apply and dries quickly.
- Rests for casting and levels well.
- 100% solids without diluents and without smell .
- Flexible and absorbs shocks and hard and violent mechanical blows and is suitable for making molds.
- If pouring materials such as leveling epoxy, coat the mold with silicone 350 in a thin layer to prevent sticking and easy separation.
uses:
- for the production of flexible molds
100% solids 100% elongation for making molds for castings
Technical data:
- Consumption for a 3 mm layer – 3 liters per square meter.
- Flexibility – 1 mm (sheen).
- Elongation – 100% <
- Density – 0.2 + 1.1 gm/cm 3
- Viscosity – 20,000 cps (Brookfield).
- Stiffness – < 10 Dg (Ericsson).
- Adhesion capacity – 620 kg/cm2.
- Mixing ratio – 3:1
- Abrasion – 120 microns – 3200 cycles (Gardner) ASTM
- Recommended layer thickness – no thickness limit but not less than 200 microns.
- Recommended number of layers – with one thick layer or unlimited additional layers in the future, only light polishing is required to prepare an area to improve adhesion between the layers.
containing:
- Special polyurethane.
- Melanins, pigments.
- Special plasticizers.
- Deep penetration materials.
- additives.
- keys.
variety:
- Standard gray or any shade as ordered (minimum 250 liters per shade).
Lightning:
- Shiny – silk.
Touch drying :
- 4 hours, final for walking – 24 hours, final difficulty – 7 days.
100% solids 100% elongation for making molds for castings
Drying between layers:
- 24 – 6 hours.
Application methods:
- casting.
Dilution:
- Do not dilute.
- To spray – dilution with thinner 11-D f
Application instructions:
- Mix part A with part B in a ratio of 3:1 thorough mixing. It is recommended to transfer to another vessel and mix again to prevent residues of unmixed material on the sides and bottom of the vessel. and
- Pour the mixture into the model at the desired thickness. and
packing:
- 1.25 + 3.75 = 5 liters, 18 liters = 13.5 + 4.5, 200 liters.
storage:
- In a cool and shady place at room temperature. and
- Make sure lids are tightly closed. and
Shelf Life:
- 12 months in the original packaging. and
Cleaning tools:
- Thinner 11-D at the end of painting. and
This technical specification is for non-binding general information only. and
Manufactured by Denber Paints and Coatings Israel Ltd. , P.O. Box 690 Sderot, 80100, certified by the Israeli Standards Institute in accordance with the ISO 9001-2015 standard
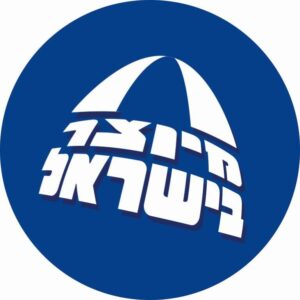
- Visit our sites: http://www.denber.net
- www.denber-paints.co.il
- www.denber-colors.co.il
- Varnish for wood. How to choose the right varnish for wood
- Thermal isolation Thermoseal 200 energy saving in green construction
- Crystal epoxy resin for tables
- Fire resistance of houses, hardwood and parquet floors, decks
- Sealing the floor of the balcony, terrace from rain
- Thin floor nano-coverings for industrial refrigerators and freezers
- Epoxy floors – Benefits of epoxy floors
- Swelling paints for steel protection against fire – Fire retardant paint
- As part of the restoration of buildings – concrete restoration at the Yad Kennedy site
- Paint for aircraft Denbergloss Jets
- Complicated sealing based on innovative technologies
- Reconstruction project of a unique house (Israeli house of architect Gaudi); Renovation of condominiums
- The work on the floor covering and restoration of the sports hall has been completed
- Denber has developed an innovative solution for thermal insulation works
- Mold, how to remove mold correctly and how to fight mold
- “Sick” buildings – Antibacterial paints destroys viruses / bacteria – Bacterinoll/ Tutgum Bacterinol
- Denber – floor coating using epoxy and polyurethane – find out what is suitable for you epoxy floor or polyurethane floor
- Epoxy floor coating and epoxy paints