Denbergloss Ship marine paint
Marine durable top coat paint for external uses up the water level.
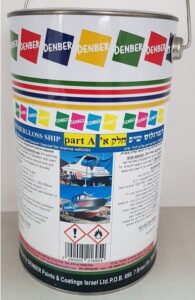
Denbergloss Ship marine paint. denber-paints.co.il
Polyurethane aliphatic two component top coat marine paint durable in salt sea environment. Hard top coat, multi-solids, UV resistant for indoor and outdoor coating. Particularly suitable for painting all the upper parts exposed to the sun and sea water of various vessels, boats, bridges over water and any object near sea exposed to salt sea vapors or in contact with sea water. Produced in many shades, and in any gloss. For top coating any marine infrastructure. Decorative smooth and durable in erosion in harsh environment, dust-resistant, can be applied in several layers. Does not fade despite long exposure to the sun.
Denbergloss Ship marine paint
Marine durable top coat paint for external uses up the water level.
Properties:
- Excellent long durability to sea water and sun.
- Durable in long exposure to sun and sea increased radiation..
- Smooth finish and Easy washing of sea salts.
- Flexible and rigid one.
- Very washable dust and dirt repellent.
- High hardness, suitable for painting items in outdoor conditions and in chemicals environment, and that needs erosion durability.
- Excellent adhesion capacity to infrastructure. Strengthen the infrastructure from hits and scratches and mechanical damage.
- Easy to implement.
- UV resistant, resistant to exterior harsh environment conditions and freezing.
- Resistance to heat and cold.
- Very high gloss or other by demand, durable for many years.
- Quick drying.
- Does not contain cadmium, lead, and chromates.
- High solids quantity, economical, suitable for painting high build layers.
- Exceeds SSPC paint 36 specification for a level 3 urethane.
Applications:
- As the upper layer for all parts of ships above water. Ordinary, decks, residential interior and exterior.
- For painting interior and exterior walls and floors of the ship.
- For areas where fire protection needed (kitchen, machine room)– Denbergloss antiflame..
- and For painting accessories & parts & elements of fiberglass and wood boats and vessels as marine coating systems.
- For painting the top layer metal parts painted epoxy
- For painting sea buoys.
- and For painting wood and metal bridges near sea water or on top of them.
- For painting all pier parts, including buildings walls.
- For painting marine accessories and parts and ground equipment on the beach.
Denbergloss Ship marine paint
Marine durable top coat paint for external uses up the water level.
Technical data:
- Part 1 –can be easily blended manually for smooth and uniform solution is 5 minutes.
- Part II – to be transparent and clear.
- Storage durability – 24 hours in 570 C without sagging.
- Theoretical coverage: 1 liter to 10-15 sqm
- Hiding power — all colors except yellow >0.95, yellow >0.9 in dry layer with thickness of 58 micron.
- Recommended thickness- 75-100 micron dry layer.
- Recommended wet layer – 120-150 micron.
- Recommended number of layers – 1-3
- Flexibility – 1 mm (Sheen)
- Density – 1.1-1.4-gm\cm3 (0.9 clear lacquer)
- Average viscosity A + B – 1-2 Pa.sec
- Viscosity glossy paints B + A – 17-23 seconds in # 2 (>95 krebs)
- Viscosity matte A+B – < 115 krebs
- Hardness – >10 Dg < (Erichsen)
- Abrasion – 120 microns – 3600 cycles (BYK Gardner)
- Ratio A:B – 2:1
- Diluted paint durability in can – 6 hours (increased viscosity of no more than 6 seconds from original viscosity)
- Grinding- glossy paints <7 Hegman, Matt <5 Hegman
Marine durable top coat paint for external uses up the water level.
- Gloss in 600 for glossy paints – >80%, for silky paints – 15-45%, for matte paints – <5%
- Shade changes allowed – Delta E –< 1.0
- Pot life = work time after mixing B + A – <4 hours.
- Distilled water resistant 24 hours – without losing adhesion or corrosion inspected 1 hour after pooling out of the liquid.
- Carbons resistance – without losing adhesion inspected 1 hour after pooling out of the liquid.
- Resistance to oil 1250 24 hours at 121OC- without losing adhesion inspected 4 hours after pooling out of the liquid.
- Resistance to hydraulic oil 24 hour in 66OC – without losing adhesion inspected 4 hours after pooling out of the liquid.
- Jet fuel resistance – 7 days in room temperature- without losing adhesion inspected 4 hours after pooling out of the liquid.
- Heat resistance durability – 121OC for 60 minutes. No color shade changes up to Delta E = < 1
- Humidity cell durability – 30 day 100% humidity temperature 49OC – without losing adhesion or damage to the film 1 hour after the release of the liquid.
- Accelerated weathering ASTM G53, ASTM D4587 – (on Epoxyden ship primer) – after 3,000 hr. lose <5% of gloss, no rust, no adhesion loses or any visual defect.
- Salt spray chamber –
- (on Epoxyden ship primer) with no rust after 3,000 hours. ASTM B117
- Thermal shock – without losing adhesion.
- Paint remover – epoxy paint remover MZ-83
- Solids content – in glossy 68% , silk and matte – >45%, clear >35%
- Impact resistance – ASTM D2794 no cracking.
- UV resistance – 1,200 hr. Q-Panel with UVA-340 lamp, 8 hr. light cycles in 60OC and 4 hr. in 50OC, according ASTM D4587-91 with no mechanical defects and color changes.
Denbergloss Ship marine paint
Marine durable top coat paint for external uses up the water level.
Contains:
- POLYOL
- Fillers, durable pigments.
- Flexibility materials.
- Special alkyd.
- Solvents, additives
- Part b – aliphatic isocyanates UV durable, special mixture.
Color :
- All RAL catalog shades.
- All FED-st. 595
Gloss:
- Glossy for all exterior parts and matte to all slipping risk areas.
Touch-dry time:
- <1 hours.
Drying time between layers:
- For an extra layer – 30 min., hard drying – 8 hours, final drying – 12-16 hours.
Application method:
- Brush, roller, spraying.
Denbergloss Ship marine paint
Marine durable top coat paint for external uses up the water level.
Dilution:
- Spraying – 35-45% thinner D-11, pressure 3-4 atm.
- Brushing/roller – you can without diluting or up to 20% thinner D-11 if a smudge lines or “orange peel” effect occurs at the time of application.
- In summer for slow down the drying and prevent OVER SPRAY recommended to add retarder.
- Airless – 0-5% D-11.
Surface preparation:
- Wooden and fiber boats – renewal: Thorough cleaning, grease, dirt and loose paint.
- Sand with glass paper or mechanical still brushes and blow with air pressure to remove dust, paint, salts and scale.
- Fill holes and sockets with Polyflex Schpachtel,flexible filler and sand for smooth surface.
- Spray a primer filler layer of Compact Schpachtel, sand lightly.
- Apply 3 coats of Denbergloss Ship.
- Metal Ships and Boats: Thorough cleaning, grease, dirt and loose paint.
- Sand with glass paper or mechanical still brushes and blow with air pressure to remove dust, paint, salts and scale.
- Fill holes and sockets with Polyflex Schpachtel,flexible filler and sand for smooth surface.
- Spray a primer layer of Epoxyden ship primer red and mid. layer Epoxyden ship primer gray (Solcoat).
- Apply 3 coats of Denbergloss Ship.
Primer paint:
- Epoxyden ship primer red and Epoxyden ship primer gray or Epoxyden Antirust Rust converter on iron rusty metal boats and ships. (a mid-layer of Epoxyden Solcoat aluminum recommended for barrier isolation before top coat painting)
- Compact schpachtel for wooden boats and ships..
Denbergloss Ship marine paint
Marine durable top coat paint for external uses up the water level.
Packaging:
- 3.35 + 1.65 = 5 liters.(ratio- 2:1), 2+0.5=2.5 liter (ratio- 4:1)
Storage:
- In a cool and shady room temperature with appropriate ventilation.
- Keep lids sealed..
Shelf life:
- 24 months in original package.
Tools cleaning:
- Thinner D-11 at the end of painting.
Quality control:
- In factory laboratories according to specifications.
- COA and COC certificate.
- ISO 9001-2015
Safety precautions:
- Inedible, keep away from the reach of children. also
- Flammable – keep distant from heated areas, fires, flames, and sparks, Prohibit smoking in working area. also
- While applying, good air ventilation is important. In case there is not enough air, use ventilation according to the ventilation table. also
- Wear protective glasses, gloves and suits. also
- Avoid direct contact of the paint and/or thinner with the eyes and skin. In case of contact, immediately wash thoroughly with water. also
- In case of an injury immediately get doctors assistance. also
- Read the safety instructions on the labels. also
- See M.S.D.S also
Denbergloss Ship marine paint
Marine durable top coat paint for external uses up the water level.
- For more information about Denber Paints and Denber Projects, please contact us by phone and/or to the company’s websites:
- company profile English also
- For more details please refer to the Denber website also
- For our Facebook page click here also
- To the Facebook page of the CEO of Denber also
- For more projects click here also
- To the article: Sealer for stone and concrete and marble also
- To the article: Thermal insulation in nanotechnology also
- article: Thermal insulation Thermosil 200 energy saving in green construction also
- Related article: Thermal insulation, floor coating also
- To the article: Thermal insulation in nanotechnology company Denber also
- Fire resistance of houses, hardwood and parquet floors, decks also
- Swelling paints for steel protection against fire – Fire retardant paint also
- Epoxy floor coating in casting and painting also
- Crystal epoxy resin for tables also
- To the article Sealing also
- The complete article on the sealing materials for roofs and walls also
- Sealing the floor of the balcony, terrace from rain also
- Mold, how to remove mold correctly and how to fight mold also
- “Sick” buildings – Antibacterial paints Bacterinoll/ Tutgum Bacterinol also
- Paint for aircraft Denbergloss Jets also
- Asphaltflex execution specification – Denber Paints also
- Denbergloss grainy car paint also
- Denbergloss Clear also
- Varnish for wood. How to choose the right varnish for wood also
- Crystal epoxy for tables from Denber also
- Paint for swimming pools, epoxy Epoxyden Dengal, performance specification also
- Color specification of quadrant helmets also
- For a free consultation, call Denber – Dr. Blen Evgenia – 050-3551549 / 050-3551551 also
- Need advice? Contact us by email: Denber@bezeqint.net or contact us at 08-9960794