Epoxyden Floor Coat Antistatic
Electric conductive floor coating
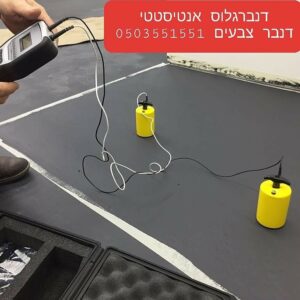
Epoxyden Floor Coat Antistatic. www.denber-paints.co.il
Two component epoxy, with electrical conductivity, to form a smooth self-leveling (without stitches) anti-static floor coating of 1-3 mm. thickness by pouring and spreading the product on the floor. The coating has excellent chemical and corrosion resistance as well as against scratches. The product is durable in harsh and extreme conditions including heavy load traffic on the surface.
Epoxyden Floor Coat Antistatic
Electric conductive floor coating
Properties:
- To ground all the electrical currents of the static electricity along the coat and through the copper stripes that is under the coating to the ground point.
- Heavy duty-thick
- Easy pouring-self
- 100% solids – no solvent
- Has alkali and acid durability according to the table
- Durable against industrial polluted water for long periods of
- Durable against fuels and
- and Durable against cleansing and other pungent
- Durable against scratches, hits and heavy
- At a thickness of 3mm the coating is suitable for floors that endure heavy logistical equipment, and at a thickness of 1 mm the coating is suitable for medium loads and for
- Covers the floor with an even and smooth coat that has no
- Easy to clean and leaves a clean floor after an ordinary
- Excellent adhering ability to Epoxyden floor antistatic primer layer.
- High mechanical strength and excellent erosion
- Durable in dry heat of up to 200°C on short periods of time and up to 100°C for long periods of time.
- Easily repairable at very low
- Doesn’t contain any thinners enabling application at minimal
Application:
- For coating floors in electronic industries that static electricity affects the equipment
- For industries that cannot tolerate a single spark that could cause
- and For a smooth coating for hi-tech industries that require high cleanliness
- For static electricity control in the production
Epoxyden Floor Coat Antistatic
Electric conductive floor coating
Technical specifications:
- Amount needed per sqm: For a thickness of 1 mm -1 liter per
- For a thickness of 3 mm – 3 liters per
- Density: 3-1.7 gm/cm3 (DIN 51575)
- Solids % – 100%
- Mixing ratio: 5:1
- Flash point: Base 255°C, hardener at 166°C (isn’t flammable , doesn’t contain solvents) (DIN ,53213 53213 )
- Hardness: > 10 Dg (ERICSON) (over 60 DIN 53153)
- Flexibility: film 120 microns – 4mm (SHEEN).
- Flex-resistance: 8 N/mm2(DIN 53452)
- Flex potency: 30 N/mm2
- Viscosity: 12,000-15,000 CPS (BROOKFIELD)
- Stretch resistance: 600kg per cm2.
- Pressure resistance: per cm2.
- Erosion endurance: 4500 cycle (Gardener) ATSM, roll CS,-17 l kg load, 1000 cycles, loss of 40 milligrams, according to ASTM 4060
- Impact resistance: 2.0 Dg/mm2
- Adhesion to concrete: stronger than the
- Adhesion to Epoxyden floor primer: 245kg per
- Flexibility in drag: 10% N/mm2 (DIN 53457)
- Drag resistance: 8 N/mm2(DIN 53455).
Electrical details:
- Surface resistance: 25-1.0 Mega ohm (ASTM F 150-89)
- Resistance to the ground without copper stripes: same as
- Resistance to the ground at a thickness of l mm: 60-425 ohm,
- and Resistance to the ground at a thickness of 3mm: 180-1500 ohm
Epoxyden Floor Coat Antistatic
Electric conductive floor coating
Contains:
- Special Epoxy resin
- Conductive fillers
- Self-leveling agents.
- Special wetting agents
- Conductive pigments
- Additives
Colors:
- Black, grey light and dark, blue-grey, green-grey, yellow-grey.
- To order other colors requires another part of the product that contains special filler (part C). This part is added to the A and B mixture and immediately colors it, using this method you can (though not recommended) get any color wanted and not add the copper
- Emphasizing the fact that the copper stripe method proved itself throughout the years as reliable, therefore the required conductance at any point on the surface has the same conduction from that point to the copper stripe l -3mm under the inspection point or max. 50 cm. from the inspection
- Though without the copper stripes conduction is required throughout all the surface until reaching the ground point that could be a great distance especially in large halls that could reach tens to hundreds of
- If static stability control is required, the copper stripes must be
Gloss :
- Silk, gloss
Touch-dry time:
- 4-8 hours at 25°C for a 1 micron
Epoxyden Floor Coat Antistatic
Electric conductive floor coating
Wait time period between layer applications:
- 12-16 Final 16-24 hours. Finish: 3-7 days (figures change according to the temperature).
Ventilation:
- Does not contain any solvents so that a medium amount of air is
Application timing of 500 micron layering:
Temperature | First appliance | Final appliance | |
7°C | 96 hours | 15 days | |
10°c | 48 hours | 10 days | |
15°C | 30 hours | 7 days daysdays | |
20°c | 24 hours | 3 days | |
30°C | 18 hours | 2 days | |
40°C | 12 hours | 1 day |
Application methods:
- Pour and spread with hard wiper and it will self-level.
Epoxyden Floor Coat Antistatic
Electric conductive floor coating
Thinning:
- No thinning
- Add a small amount in order to chill the mixture if a heat reaction has accord preventing it from drying quickly and increasing its pot
Surface preparations:
- It is required to apply on the Epoxyden floor primer surface only if it is completely clean and
- It is possible to repair small and large surfaces with grout epoxy before applying Epoxyden floor
Electric conductive floor coating
Instructions:
- Spread a thin layer Epoxyden floor primer (antistatic black) over the entire surface according to the instructions manual for the product, wait 24 hours till it The mixture ratio of the primer is 2.5:1 or 1:1 and reacts exactly like paint, easy to apply and is suitable for applying the copper stripes on.
- Apply/glue the copper stripes all over the primer surface in 1 meter distance between the lines. Glue them horizontally and vertically.
- With a brush using the Epoxyden floor primer as glue cover totally all the copper strips.
- At the edges of the surface weld those connecting copper wires to the It is recommended to have four different connects to the ground.
- Make sure that the primer layer is completely dry and clean from dust, dirt and grease free. Check if the copper stripes stuck well to the primer and the welding is The welding stains should be removed carefully with degerizer M without damaging the primer layer. Any damage must be repaired. Therefore waiting needed until it completely dries.
- Open carefully sections A and B of the Epoxyden floor antistatic and pour the required amount according to the ratio of 5:1 (for example for a thickness of l mm it is required to prepare 1 liter mixture per 1 sqm. surface. Therefore to cover a 10 sqm. surface requires 10 liters of mixture)
- Stir the mixture well then immediately pour the mixture on the edge of the surface
- With a large rubber wiper spread the mixture evenly coating the floor according to the calculation in the required thickness.
- It is recommended not to move any heavy equipment such as forklifts or trucks on the floor before at least a week has passed after the
Epoxyden Floor Coat Antistatic
Electric conductive floor coating
Static electricity created by walking on the floor (average figures):
- Isolated shoes: 60-150
- Leather shoes: 12-50 volts
- Special plastic antistatic shoes: 10-30
Uploading time period (of 500 volts) of static electricity that form while walking with these shoes:
- Isolated shoes: 3-8
- Leather shoes: 25-2.5 seconds
- Special plastic antistatic shoes: 05-1 seconds.
Life span after mixture (POT LIFE) according to the temperature:
5 liters of A +B mixture | |
10°C | 1 hour |
15°C | 45 min. |
20°c | 30 min. |
25°C | 25 min. |
30°C | 20 min. |
35°C | 15 min. minutes |
Package:
- 3.4+1.6=5 liters, 5+13= 18 liters
Epoxyden Floor Coat Antistatic
Electric conductive floor coating
Storage:
- Store in a shaded place, at a temperature of between 15°C-32°C with proper ventilation.
- Keep lids tightly closed.
Shelf life span:
- 24 months in its original
Equipment cleansing:
- Use D-4100 thinner immediately after
Quality control:
- In factory laboratories according to specifications.
- COA and COC certificate.
- ISO 9001-2015
Safety precautions:
- Inedible, keep away from the reach of children.
- Flammable – keep distant from heated areas, fires, flames, and sparks, Prohibit smoking in working area.
- While applying, good air ventilation is important. In case there is not enough air, use ventilation according to the ventilation table.
- Wear protective glasses, gloves and suits.
- Avoid direct contact of the paint and/or thinner with the eyes and skin. In case of contact, immediately wash thoroughly with water.
- In case of an injury immediately get doctors assistance.
- Read the safety instructions on the labels.
- See M.S.D.S
Epoxyden Floor Coat Antistatic
Electric conductive floor coating
- For more information about Denber Paints and Denber Projects, please contact us by phone and/or to the company’s websites:
- company profile English also
- For more details please refer to the Denber website also
- For our Facebook page click here also
- To the Facebook page of the CEO of Denber also
- For more projects click here also
- To the article: Sealer for stone and concrete and marble also
- To the article: Thermal insulation in nanotechnology also
- article: Thermal insulation Thermosil 200 energy saving in green construction also
- Related article: Thermal insulation, floor coating also
- To the article: Thermal insulation in nanotechnology company Denber also
- Fire resistance of houses, hardwood and parquet floors, decks also
- Swelling paints for steel protection against fire – Fire retardant paint also
- Epoxy floor coating in casting and painting also
- Crystal epoxy resin for tables also
- To the article Sealing also
- The complete article on the sealing materials for roofs and walls also
- Sealing the floor of the balcony, terrace from rain also
- Mold, how to remove mold correctly and how to fight mold also
- “Sick” buildings – Antibacterial paints Bacterinoll/ Tutgum Bacterinol also
- Paint for aircraft Denbergloss Jets also
- Asphaltflex execution specification – Denber Paints also
- Denbergloss grainy car paint also
- Denbergloss Clear also
- Varnish for wood. How to choose the right varnish for wood also
- Crystal epoxy for tables from Denber also
- Paint for swimming pools, epoxy Epoxyden Dengal, performance specification also
- Color specification of quadrant helmets also
- For a free consultation, call Denber – Dr. Blen Evgenia – 050-3551549 / 050-3551551 also
- Need advice? Contact us by email: Denber@bezeqint.net or contact us at 08-9960794