Epoxyden Strontium Chromate
Anticorrosive and converts rust
Two component primer paint, high solids content, anticorrosive and converts rust, strontium chromate base for iron metals and aluminum. EPOXYDEN PRIMER STRONTIUM CHROMATE-ANTICORROSIVE TWO COMPONENTS FOR IRON METALS AND ALUMINUM.
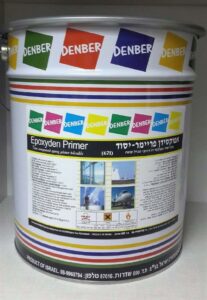
Epoxyden Strontium Chromate. www.denber-paints.co.il
Element of strontium chromate used as rust converter rich with zinc phosphate, particularly strong with a unique molecular structure. manufactured in accordance with the requirements of the contents of zinc and chromates, cadmium is prohibited and lead content max. 0.06%, tints as listed in standard strontium chromate greenish gray tint.
Paint creates a primer foundation layer with high adhesion to parts that maid of iron metals and aluminum. Parts treated according to the U.S. Fed. St. Also used as the mid. layer “bridges” the old paint before you recoat with a polyurethane top aliphatic paints.
Epoxyden Strontium Chromate
Anticorrosive and converts rust
Properties:
- Primary paint with high mechanical strength and adhesion to iron metals, galvanized steel and treated aluminum.
- Creates a suitable preparation for top painting polyurethane aliphatic paints.
- Anticorrosive and rust converter.
- Durable in alkaline and acids mixed with a salt and moisture environment.
- An excellent adhesion to infrastructure.
- Suitable also as bridge coat to old paint coat before repainting new layer of paint.
- Easy to apply and dries quickly.
- Ready to recoat and/or top layer coating on the same day after 12 hours.
- High coverage.
- Durable in jets gasoline and oils.
Applications:
- As the basis for paints interior and exterior aluminum parts, iron and galvanizes metals.
- For strengthening infrastructure before coating top layer and as intermediate layer.
- Primer coat before coating iron and treated aluminum with proper top coat.
Technical data:
- Coverage – 1 liter to 16 sqm. in a layer of 50 microns dry.
- Flexibility – 1 mm ( sheen )
- Density – part A 1.35-1.45 gm\cm 3, part B 85 -0.95 gm\cm 3
(ASTM D 1475)
- Viscosity – part A + part B immediately after mixed 40 seconds cups4 #
- Hardness – >10 Dg (Erichsen)
- Flash point- 38 o c
- Amount of solids part A – by weight 68%, part B – by weight 52% ( ASTM-D-2369 )
- Erosion-120 microns-2260 cycles (Gardner) ASTM
Epoxyden Strontium Chromate
Anticorrosive and converts rust
- Recommended layer thickness – 15-23 microns dry (minimum values)
- Recommended layers – at least 2
- Touch dry time – up to 5 hours.
- Hard dry time – up to 8 hours.
- Pot life (once- mixed A+B) – 4 hours. ( after 4 hours the blend A + B viscosity will be less than 70 seconds on # 4, after 8 hours the mixture will not create jells)
- Mixing ratio a: b – 2.5: 1 in volume.
- Waiting time after mixed and before starting painting: 10 minutes and blend again with a mechanical mixer.
- Heat tolerance durability – at 121O C, over 1 hour without any changes in the quality of the film and the hue color.
- Hot oil durability – 121 O C 24 hours without any changes in the quality of the film and the hue color.
- Resistant hydraulic oil – 65 O C 24 hours without any changes in the quality of the film and the hue color.
- Solvents durability – 50 time rubbing cloth marriages in MEK with no peel off paint.
- Distilled water durability – for 4 days in 49 O C – with no defects of film.
- Masking tape adhesion test – pressed with barbell 2 kg for 1 hour and rip of -no flaking of paint rip of.
- Removes paint – 90% or more in 60 minutes in paint remover.
- Salt spray – durable >2000 hours.
Contains:
- Epoxy resin.
- Fillers, strontium chromate pigments.
- Polyamide hardeners
- Phosphate zinc.
- Fillers.
- Additives.
Epoxyden Strontium Chromate
Anticorrosive and converts rust
Color:
- Yellow greenish
Gloss:
- < 5% (ASTM D 523 ) test camouflage paints in 60 0 lens
Dry to touch:
- 12 minutes to 5 hours. (Due to the fast drying avoid over spray “dust”)
Dry in between the layers:
- 6-8 hours. Complete drying: 8 hours.
Application methods:
- Roller, brush, spray gun, airless.
- Air gun – in pressure 4 atm.
- Airless- 0-5% dilution nozzle “0.021
Dilution:
- Thinner D-4/100 . (corresponding to MIL-T-81771 Type II )
- 10-25% according to need for roller or brush. appearance of the “orange” shell, you can increase the dosage to 35%
- Air spray gun – 10-25% thinner D-4/100
- Airless – 0-5% thinner D-4/100
Epoxyden Strontium Chromate
Anticorrosive and converts rust
Surface Preparation:
- Clean surface from dust, fat, dirt and loose paint.
- Old coat – sand well and clean with dry air, clean with clean rag dipped in thinner.
- Aluminum alloy/aluminum exposed or new – treatment of chemical burn and passivation according to space preparation devices: MIL-C-5541 MIL-C-81706
- Iron metals – sand blasting cleaning up to SA- 2.5 standard (white metal)
- Very large parts – remove paint with paint removers and flash with water, spray plastic soft granular to complete stripping and rinse thoroughly and dry.
Top color:
- You can paint top color on primer 8-12 hours after painting. If primer was spread in appropriate conditions.
- During cold winter you can paint after 24 hours.
- The matching paints are all types of aviation top layer paints for aircraft and space including CARC paints.
Instructions for use:
- Open carefully parts A and B and mix separately.
- Pour two parts A and 1 part B to the required amount and mix well with mechanical mixer (recommended air mixer) for a uniform mixture.
- Wait 10 minutes while adding thinner and mix again.
- Pour to painting equipment and spray thin layer for at least 23 microns dry. If necessary if the layer is not uniform or part not painted perfectly, wait approximately 4 hours (up to 12 hours if not dry completely you will receive a shrinked layer) and spray another layer.
- Insert into sealed and clean and dry room with temperature control for 12 hours before paint overlay.
- Clean equipment after work.
Pot Life after mixing a blend of A+ B of 5 liters:
- 15 O C – 10 hours
- 20 O C – 8 hours
- 25 O C – 6 hours
- 30O C – 5 hours
- 35 O C – 4 hours
Epoxyden Strontium Chromate
Anticorrosive and converts rust
Ventilation:
- Amount of air required for 1 liter epoxyden primer blend:
- Or 10% of LEL = 65 M 3
- For the TLV = 990 M 3
Package:
- 4 + 1 = 5 liters.
Storage:
- In a cool, shaded room with proper ventilation.
- Keep lids tightly closed.
Shelf life:
- 12 months in the original packaging.
Cleaning tools:
- Thinner D-4/100 as soon as finish the painting.
Quality control:
- In factory laboratories according to specifications.
- COA and COC certificate.
- ISO 9001-2015
Epoxyden Strontium Chromate
Anticorrosive and converts rust
Safety precautions:
- Inedible, keep away from the reach of children.
- Flammable – keep distant from heated areas, fires, flames, and sparks, Prohibit smoking in working area.
- While applying, good air ventilation is important. In case there is not enough air, use ventilation according to the ventilation table.
- Wear protective glasses, gloves and suits.
- Avoid direct contact of the paint and/or thinner with the eyes and skin. In case of contact, immediately wash thoroughly with water.
- In case of an injury immediately get doctors assistance.
- Read the safety instructions on the labels.
- See M.S.D.S
Anticorrosive and converts rust
- For more information about Denber Paints and Denber Projects, please contact us by phone and/or to the company’s websites:
- company profile English also
- For more details please refer to the Denber website also
- For our Facebook page click here also
- To the Facebook page of the CEO of Denber also
- For more projects click here also
- To the article: Sealer for stone and concrete and marble also
- To the article: Thermal insulation in nanotechnology also
- article: Thermal insulation Thermosil 200 energy saving in green construction also
- Related article: Thermal insulation, floor coating also
- To the article: Thermal insulation in nanotechnology company Denber also
- Fire resistance of houses, hardwood and parquet floors, decks also
- Swelling paints for steel protection against fire – Fire retardant paint also
- Epoxy floor coating in casting and painting also
- Crystal epoxy resin for tables also
- To the article Sealing also
- The complete article on the sealing materials for roofs and walls also
- Sealing the floor of the balcony, terrace from rain also
- Mold, how to remove mold correctly and how to fight mold also
- “Sick” buildings – Antibacterial paints Bacterinoll/ Tutgum Bacterinol also
- Paint for aircraft Denbergloss Jets also
- Asphaltflex execution specification – Denber Paints also
- Denbergloss grainy car paint also
- Denbergloss Clear also
- Varnish for wood. How to choose the right varnish for wood also
- Crystal epoxy for tables from Denber also
- Paint for swimming pools, epoxy Epoxyden Dengal, performance specification also
- Color specification of quadrant helmets also
- For a free consultation, call Denber – Dr. Blen Evgenia – 050-3551549 / 050-3551551 also
- Need advice? Contact us by email: Denber@bezeqint.net or contact us at 08-9960794