Polyflex 225A Schpachtel filler Floor cracks and expansion stitches
Flexible 2K polyurethane heavy duty mastica
For big cracks and concrete stitches. High build super flexible polyurethane.
Polyflex 225A schpachtel is made from special polyurethane, double component, for thick flexible spreading to fill cracks or horizontal and vertical surfaces, is highly adhering to all types of hard infrastructure.
Applicable on industrial concrete and asphalt surfaces, suitable for spreading and repairing over industrial equipment damage and especially used at places where extreme chemical endurance is required. Endures fuels, diluters and chemicals in the toughest and harshest conditions. Has no width limitation. Noise and mechanical hit resistant. Has excellent erosion endurance. Applicable directly into cracks, splitting slits, breaks, peelings, different holes, and between different metal layers enabling sealing, noise resisting, gluing, that endures intense vibrations. Its molecular structure creates its flexibility that prevents breaks and cracks that are caused from erosion.
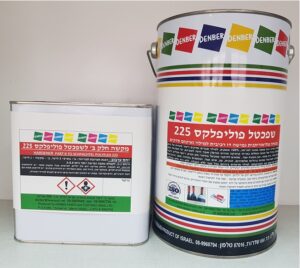
Polyflex 225A Schpachtel filler Floor cracks & expansion stitches. www.denber-paints.co.il
Polyflex 225A Schpachtel filler Floor cracks and expansion stitches
Flexible 2K polyurethane heavy duty mastica
Properties:
- Heavy duty-thick One layer applicable at any width desired. 100% solidity – no solvent evaporation.
- Has alkali acid durability. Durable against industrial polluted water for long periods of time. Durable against fuels, oils, lubricates and jet fuels.
- Durable against cleansing and other pungent Durable against scratches, hits and heavy loads.
- Amazingly flexible and resilient, return back to its original shape without any Has an excellent adhering ability to concrete and aluminum surfaces and all types of industrial infrastructure.
- High mechanical strength and excellent erosion durability.
- Durable in dry heats of up to 120°C on short periods of time and up to 80°C for long periods of time.
- Does’nt contain any thinners so it is applicable in low ventilation Quiets noises and creates an acoustic.
- Appropriate for chemical industrial equipment to fill, seal and to resist Appropriate for repairing tanks and pools avoiding future leaks caused by expansion and shrinking.
Flexible 2K polyurethane heavy duty mastica
Applications:
- To repair and coat floors, walls, stairs, airport parking lots, hangers, warehouses and etc.
- To coat horizontal and vertical fuel reserve surfaces, chemical caches, chemical stockpile containers, oxidization and submerging containers, industrial waste stockpiles and industrial sewage pools.
- To coat, repair and protect steel walking surfaces, for isolation and silencing in chemical factories where corrosive materials are used.
- To coat noisy carts running lans.
- To coat chemical industrial floors for chemical endurance.
- To fill in spreading cracks in food, medicine and chemical industries to obtain perfect isolation, and a sanitary environment, to protect against penetrating materials and preventing critical damage to industrial floors.
- To fill in small and large cracks with a flexible substance, for concrete floors, concrete and metal walls in factories, garages, warehouses and etc.
- To fill connection beams made from cement and aluminum, endures ground movements, shocks and constant vibrations.
- For oil and water wet work surfaces.
- For aviation use between and on aluminum surface connections improving the connection, seals and prevents noise.
- For sealing gaps in tube passages that run through containers and different metal and concrete walls.
- For filling noisy gaps between different fluctuating metals.
- For filling gaps created in vibrating machines, and between metal plates for strengthening and sealing.
Polyflex 225A Schpachtel filler Floor cracks and expansion stitches
Flexible 2K polyurethane heavy duty mastica
Technical specifications:
- Amount needed: 100% solids, casting volume is equal to the substance volume.
- Density: Base (section A) gray color: 1.3 gm/cm3 (DIN 51575) RAL7032
- Hardener (section B) clear color: ,1.22 A+B mixture: 23.3+6.7=30 Kg
- Amount of solids -100%
- Bases to Hardener volume mixture ratio: 3:1
- Flash point: Base at 255°C, hardener at 166°C (isn’t flammable, doesn’t contain solvents) (DIN 53213 53213 )
- Hardness: 10 Dg (Erichsen) (over 60 – DIN 53153)
- Flexibility: film 120 microns – 1 mm (Sheen).
- Viscosity: Base (section A) 5,000-15,000 CPS (Brookfield) at 25°C Hardener (part B) 85-100
- Stretch dexterity: 600 kg per cm.
- Erosion endurance: 4500 cycle (grinder) ATSM, roll CS,-17 lkg load, 1000 cycles, Lose of 40 milligrams, according to ASTM 4060 standard.
- Adhesion to concrete: stronger than the concrete.
- Adhesion to Epoxyden Floor Primer: 245kg per square cm.
- Flexibility in drag 10% N/mm2 (DIN 53457)
- Drag resistance: 8 N/mm2(DIN 53455).
- Level of electric isolation: 15×1013ohm per cubic cm.
- Pot life time limit after mixing sections A+B: 60 minutes at 20°C.
- Minimal ripe-time before usage: at least 24 hours
- Final hardness: 3-7 days.
Contains:
- Polyurethane resin mixture.
- Chemical endurance additives.
- Hardeners.
- Additives.
- Fillers.
- Pigments.
Shades:
- Grey.
Gloss:
- Silk
Polyflex 225A Schpachtel filler Floor cracks and expansion stitches
Flexible 2K polyurethane heavy duty mastica
Touch-dryness:
- 2-4 hours at 25°C for a 500 micron layer.
Wait time period between layer applications:
- 12-16 Final 16-24 hours. (figures change according to the temperature).
Ventilation:
- Does not contain any solvents so that a medium amount of air is reuired.
Application methods:
- Casting, spreading and smooth with a spatula.
Surface preparations:
- Concrete- Apply on absolutely clean It is required to apply Epoxyden Primer first (see product specifications), if the concrete absorbs the primer leaving the surface with opened pores it is required to apply another layer of Epoxyden Primer.
- Asphalt-Clean thoroughly with high water pressure until obtaining an absolutely clean (wait till it dries completely)
- Aluminum – Apply primer Epoxyden Strontium Chromate (see product specifications) Steel-Apply a thin 50 micron layer of Epoxyden .19
- Also applicable without any primers but requires thorough sand cleansing or chemical etching into the steel metals.
Instructions:
- Make sure that the base layer is dry, clean – dirt, dust and grease free.
- Open carefully A +B sections of the Schpachtel Polyflex 225A B and pour at the base hardener ratio 3:1 the required amount according to the volume = surface calculation for double layer coating.
- Stir well with a slow mixer and spread it on the surface with a suitable spreading tool.
Package:
- 4.5+13.5 =18 liters.
Storage:
- Store in a shaded place, at a temperature of between 15°C-32°C. with appropriate ventilation.
- Keep lids tightly closed.
Polyflex 225A Schpachtel filler Floor cracks and expansion stitches
Flexible 2K polyurethane heavy duty mastica
Self life span:
- 24 months in its original package.
- Hardener-12 months.
Equipment cleansing:
- Use D-11 thinner immediately after
Quality control:
- In factory laboratories according to specifications.
- COA and COC certificate.
- ISO 9001-2015
Polyflex 225A Schpachtel filler Floor cracks and expansion stitches
Safety precautions:
- Inedible, keep away from the reach of children.
- Wear protective glasses, gloves and suits.
- Avoid direct contact of the paint and/or thinner with the eyes and skin. In case of contact, immediately wash thoroughly with water.
- In case of an injury immediately get doctors assistance.
- Read the safety instructions on the labels.
- See M.S.D.S
Flexible 2K polyurethane heavy duty mastica
Warnings:
- Don’t mix the product with materials which were not recommended by us.
- Don’t apply if the temperature is under +7°C.
- Don’t apply if humidity is over 80%
- Read thoroughly the technical data of the product listed in this section; confirm that everything is understood completely, for clarification contacts our tech. department.
- All information that is listed in this content is a recommendation merely and cannot be applied in the court of law.
- The costumer must test & check that this product is compatible with his equipment and needs.
- The information listed in this section is according to the laboratory conditions (temperature, humidity etc.) which the products were tested.
- The recommendations listed do not hold any responsibility for this product.
- Theoretical and actual coverage area are different concepts, the actual coverage is affected by the required thickness of the layers, required number of layers, painting conditions including the amount of paint which spread in the air before touching the surface.
- The information listed in this section is based on experience and accumulating data, Denber inc., has the right to change the information listed at any time.
- Paints that have been in stagnation or exposed to air more than needed could have their qualities changed.
Polyflex 225A Schpachtel filler Floor cracks and expansion stitches
Flexible 2K polyurethane heavy duty mastica
- For more information about Denber Paints and Denber Projects, please contact us by phone and/or to the company’s websites:
- company profile English also
- For more details please refer to the Denber website also
- For our Facebook page click here also
- To the Facebook page of the CEO of Denber also
- For more projects click here also
- To the article: Sealer for stone and concrete and marble also
- To the article: Thermal insulation in nanotechnology also
- article: Thermal insulation Thermosil 200 energy saving in green construction also
- Related article: Thermal insulation, floor coating also
- To the article: Thermal insulation in nanotechnology company Denber also
- Fire resistance of houses, hardwood and parquet floors, decks also
- Swelling paints for steel protection against fire – Fire retardant paint also
- Epoxy floor coating in casting and painting also
- Crystal epoxy resin for tables also
- To the article Sealing also
- The complete article on the sealing materials for roofs and walls also
- Sealing the floor of the balcony, terrace from rain also
- Mold, how to remove mold correctly and how to fight mold also
- “Sick” buildings – Antibacterial paints Bacterinoll/ Tutgum Bacterinol also
- Paint for aircraft Denbergloss Jets also
- Asphaltflex execution specification – Denber Paints also
- Denbergloss grainy car paint also
- Denbergloss Clear also
- Varnish for wood. How to choose the right varnish for wood also
- Crystal epoxy for tables from Denber also
- Paint for swimming pools, epoxy Epoxyden Dengal, performance specification also
- Color specification of quadrant helmets also
- For a free consultation, call Denber – Dr. Blen Evgenia – 050-3551549 / 050-3551551 also
- Need advice? Contact us by email: Denber@bezeqint.net or contact us at 08-9960794