Spray Antifouling marine paint
Antifouling paint
SPRAY Antifouling – high build self eroding (polishing) paint, Contain 99% pure copper and copper oxide (contain no tin) for coating the underwater parts of low (L) and fast speed (H) boats/ships.
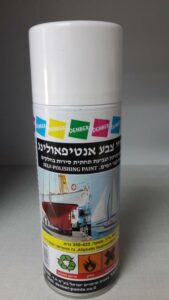
Spray Antifouling marine paint www.denber-paints.co.il
A one component paint with self abrasion and self-regeneration. With a high smoothing coefficient due to the process of hydro gel formation in the process of hydrolysis of seawater with the silicone in the paint and rediscovered with the erosion of the layers the acrylic binder is the base of the paint. The penetration of the water creates a hydro gel that weakens the shell of the acrylic layer and creates the slippery gel that allows the ship to slide in the water and erosion of the paint and regenerate in the process. For lower cruising (L) and fast (H) vessels, at the bottom below sea level, to prevent adhesion and accumulation of fowl, crops, algae, oysters, etc.,
Contains a high concentration of red or blue cuprum oxide per copper powder 99% to improve performance at low cruising speeds, these toxins are long-lasting until all 3 layers of the paint are removed. 3 layers of 100 microns each give the vessel protection for up to 3 years or more. (For protection for many more years, use copper Antifouling Epoxyden).
Spray Antifouling marine paint
Antifouling paint
Features:
- Environmentally friendly and does not contain tin compounds.
- In the process of hydrolyzing silicon in water, a slick hydro gel creates a slick hydro gel that gives the ship as minimal friction as fish skin, this slipperiness can contribute to fuel savings of 4-15%.
- Rich in copper and copper icings and provides protection from various cycling and crops on the bottom of the vessels at high and slow speeds of the vessel.
- Very strong adhesion to the primer layers of Epoxyden Solcoat.
- Contains a toxin that prevents tumor development in the underwater part of the vessel, which slows the vessel’s cruising speed while wasting a lot of energy to overcome unnecessary friction).
- Fast and thick drying can be applied in several layers for desired thickness for prolonged protection.
- Short inter layered waiting time due to the rapid drying.
- Excellent inter layered connecting ability.
- Has self-abrasion properties that reveal a fresh new layer each time without a cumulative vernical.
- Resistant to heat and cold and extreme sea conditions in salty seawater and fresh water.
- Adapted for friction in seawater at slow cruising speed (L), or fast (H), is not resistant to rough friction in the ice and/or dock walls.
- Flexible and strong and suitable for immersion conditions in seawater and fresh water for many years and to the shocks that the characteristics of the vessel receive.
- Easy to apply in the splash/roller.
- Drying up quickly. 4 layers of 100 microns can be applied one at a time for durability of 3 years or more. .
Uses:
- Paint all types of vessels small and large made of steel/fiberglass/wood/aluminum in the underwater part.
- For the painting of yachts, toweds, router and service boats, barges, race and fishing boats, fishing and cargo ships, passenger ships and cargo ships, etc.
Antifouling paint
Technical data:
- Theoretical coverage capacity – 1 liter per 15-20 square meters
- Practical consumption per layer of 100 microns – 150 ml of color per square meter for 100 microns of dry layer (minimum required).
- Should have 3 minimum layers as the specification – 1 liter to 2 square meters
- Several layers is recommended – at least 3 of 100 dry microns each. (for durability up to 3 years)
- % solid in volume – 66% (T.I.785 Part 17).
- Color pigment content – 65% (TA 785 Part 19)
- Flexibility – 1 mm (sheen) meets the examination of Israeli standard 935 section 307.
- Grinding minutes – up to 50 microns (T.I. 785 Part 15 – up to 60 mick)
- Density – 1.5-1.7 gm\cm3
- Resistance to immersion in water – no bubbles, no softening, no change in adhesion, (T.I.935 Section 312)
- Resistance to “sweating” (bleeding)- No less than level 6 according to ASTM D-868 and ASTM D-969
- Resistance to Solvents and Fuels – Durable according to ASTM D-2792-93
- Viscosity – Room Temperature Room 3.0-3.5 Pa.sec (HAAKE) 110-120 Krebs in 200 rounds per minute after manual mixing of 2 minutes (T.I. 935 Section 935 Section 302), after diluting 10% in the thinner – 85-90 Krebs. After 10 days it is stored at 42ºC – the position will increase to 5 Krebs.
- Hardness – 3 Dg< (Erickson)
- Abrasion – 120 microns – 250 cycles (Gardner) ASTM, American standard ASTM D4060 dry film thickness 200 microns, weight loss – 2 g per 500 cycles (device – up to 2.5 g licensed loss)
- Peeling strength – minimum 5 kg per square meter.
- Heat resistance up to 70 °C without change in features and deformation.
- Recommended layer thickness –150-180 microns wet.
- Recommended number of layers – 3-4.
- Flash point – 25ºC
- Drying time before sailing – 24 hours in the shade (without exposure to the sun that damages the paint and damages the quality of its activity to release the toxin)
Spray Antifouling marine paint
Antifouling paint
Contains:
- Self polishing acrylate suitable for this purpose.
- Fillers, chlorinated rubber,
- Pigments and toxins in red/brown or blue Cuprum oxide.
- Pure copper powder 99%
- Special flex materials.
- Solvents, additives.
Hue:
- Marina blue, black or red brown.
Gloss:
- Matte up to 18%, (T.I.935 Section 309).
Drying to the touch:
- 30-60 minutes depending on the temperature of the environment. Drying time on the wheel – (T.I.935 Section 304 Amendment No. 2) – up to 45 minutes
- Due to the color of acrylic type drying quickly, if an OVER SPRAY “dust” is created at the time of spraying, that is, the color dries in the air before reaching the painted surface of the vessel, which must be reached wet, the painting process must be stopped immediately, since the color accumulates on the surface painted as dry grains and these will fall out together with all layers even those that will come later on the first voyage. To prevent over spray, a number of actions should be taken: 1. Work at an environmental temperature as much as 15-30 degrees as possible even if it is necessary to paint only in the mornings or evenings. 2. Dilute the color mixture with more than a thinner and even add a retarder (drying inhibitor), if due to the thinning a layer of 100 microns is not obtained – add more layers and not settle for 3 layers until you receive a minimum dry thickness of at least 300 microns. 3. Reduce the splash pressure and work closer to the hull 20-25 cm for a gentle and uniform color fog that lands completely wet on the painted area.
Antifouling paint
Drying between layers:
- 2-4 hours, Final: 6-8 hours (depending on the temperature of the environment)
- Water insertion: Minimum 24 hours drying in the shade from the end of the last layer painting.
Application methods:
- Brushing, rolling, spraying in a spray gun or airless, electrostatic spraying.
Preparation of the area:
- Thorough cleaning of the color layer on which dust, fat, dirt, it is recommended to rinse with a Z grain to remove fats if any, rinsing with fresh water and waiting to dry, to ensure cleanliness of the area before painting.
Packaging:
- 0.4 liters.
Storage:
- In a cool, shady place at room temperature.
Shelf life:
- 12 months in the original packaging.
Cleaning tools:
- Thinner 18-D immediately after painting.
Antifouling paint
Safety:
- Not edible, out of reach of children.
- Flammable, away from heats, fire and sparks.
- Ensure proper ventilation during application.
- Wear goggles, solidarity gloves, protective clothing.
- In case of injury , seek medical attention immediately.
Caution:
- Do not paint the Antifouling paint in the sun, paint in a cool, shady place.
- Exposing the Acrylate to a direct sun will cause excessive drying of the paint peel to prevent it from functioning properly as SELF POLISHING and exposing a new toxic layer each time.
- Do not mix with unsalted ingredients.
- Do not paint this paint on visible metal. Only according to the specifications on layers of basic and medium color.
- Quality results are obtained only when all layers have been applied as specifications.
- Any deviation from the specification is at the user’s responsibility.
- Do not paint with high environmental heat and it is recommended to paint shady place and only and late morning and early evening.
- Recommended in heats not exceeding 30 degrees and humidity of up to 50%.
- Avoid contact with the skin and eyes, causing dryness and irritation of the skin. In contact, rinse with plenty of running water and seek medical attention.
- Aerosol Spray is a pressure tank, it must be emptied of gas before being thrown in the trash. It should not be thrown into the fire. There is a risk of exploding.
Quality audit:
- In our factory laboratories in accordance with iso 9001-2015 specifications
Antifouling paint
User attention:
- This technical specification is for general non-binding information only. The product is a professional product for professionals only who have already acquired previous experience in its implementation. This specification does not serve as a substitute for advice/training by an authorized consultant/guide. It is mandatory to apply to a small area for match testing first before applying large areas. The content of this specification changes over time and updates are entered, and updated versions must be requested. Names of consultants/professional instructors can be obtained by telephone. Read product MSDS safety instructions before starting work with it. Manufactured by Denver Colors & Coatings Israel Ltd., 80100 Sderot, 80100, certified by the Standards Institution of Israel in accordance with ISO 9001-2015 standards.
Spray Antifouling marine paint
Antifouling paint
- For more information about Denber Paints and Denber Projects, please contact us by phone and/or to the company’s websites:
- company profile English also
- For more details please refer to the Denber website also
- For our Facebook page click here also
- To the Facebook page of the CEO of Denber also
- For more projects click here also
- To the article: Sealer for stone and concrete and marble also
- To the article: Thermal insulation in nanotechnology also
- article: Thermal insulation Thermosil 200 energy saving in green construction also
- Related article: Thermal insulation, floor coating also
- To the article: Thermal insulation in nanotechnology company Denber also
- Fire resistance of houses, hardwood and parquet floors, decks also
- Swelling paints for steel protection against fire – Fire retardant paint also
- Epoxy floor coating in casting and painting also
- Crystal epoxy resin for tables also
- To the article Sealing also
- The complete article on the sealing materials for roofs and walls also
- Sealing the floor of the balcony, terrace from rain also
- Mold, how to remove mold correctly and how to fight mold also
- “Sick” buildings – Antibacterial paints Bacterinoll/ Tutgum Bacterinol also
- Paint for aircraft Denbergloss Jets also
- Asphaltflex execution specification – Denber Paints also
- Denbergloss grainy car paint also
- Denbergloss Clear also
- Varnish for wood. How to choose the right varnish for wood also
- Crystal epoxy for tables from Denber also
- Paint for swimming pools, epoxy Epoxyden Dengal, performance specification also
- Color specification of quadrant helmets also
- For a free consultation, call Denber – Dr. Blen Evgenia – 050-3551549 / 050-3551551 also
- Need advice? Contact us by email: Denber@bezeqint.net or contact us at 08-9960794