Denbergloss Polyester HD – polyurethane polyester Armored
Polyurethane polyester with fiberglass fibers
DENBERGLOSS POLYESTER HD – POLYURETHANE POLYESTER
TWO COMPONENT CHEMICALS RESISTANT, FOR SMALL/LIGHT
AIRPLANES, GLIDERS, FIBER TANKERS, SURFBOARDS ETC
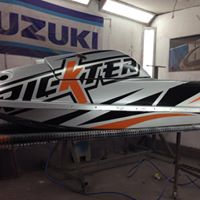
Denbergloss Polyester HD. www.denber-paints.co.il
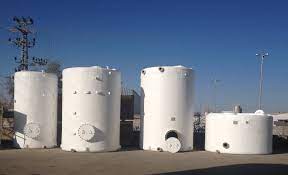
Denbergloss Polyester HD. www.denber-paints.co.il
Denbergloss Polyester HD – polyurethane polyester Armored
Polyurethane polyester with fiberglass fibers
high build for light air crafts and tankers of fiberglass
Chemical-resistant aviation and industrial polyurethane polyester color, two-component or three-component with fibers. multi-solids, UV-resistant polyurethane paint, for resistance in extremely harsh conditions, spray able plus polyester fibers for armor and reinforcement, especially suitable as a top color for light aircraft, pilots, gliders, fiberglass tanks, surfboards, various polyester elements in the military, civilian, marine and air field polyester. lead and chrome free.
Features:
- Color resistant to chemicals, thinners, acids and alkalys.
- Extremely smooth and hard finish, spray able with polyester fiber for armor and reinforcement.
- Flexible and tough as one.
- Doesn’t crack in bending.
- Very washed and well stumbled in foreign conditions for many years.
- For regular painting as a decorative top coat and as a coat that creates a reinforcement layer with fibers.
- High hardness, suitable for light aircraft, pilots, gliders, etc.
- Strengthens the color system against injuries and scratches.
- Excellent adhesion capacity for infrastructure.
- Resistant to scratches and mechanical injuries.
- Easy to implement. UV-resistant.
- Heat and cold resistance.
- Very high lightning or other on demand.
- Quick drying.
- Contains no cadmium, and contains lead up to %06 lead. Contains no chromates.
Uses:
- As an upper layer for light aircraft, drones, drones, airplanes, gliders made from polyester/fiberglass or lightweight complex materials.
- For painting surf boards, marine coatings, vessels made of fiberglass, etc.
- For painting fiberglass containers.
- and For painting elements of communication from fiberglass.
- For painting fiberglass enclosures, plastic and fiberglass facilities.
- To paint large storage tanks plus fiber for strengthening.
Denbergloss Polyester HD – polyurethane polyester Armored
Polyurethane polyester with fiberglass fibers
Technical data:
- Part 1 – Manual mixing can be easily mixed and after 5 minutes a uniform and smooth solution will be obtained.
- Part 2 will be transparent and clear.
- and Part C – fiber.
- Storage durability – 24 hours at 570 without separations and spoilage,
- theoretical coverage – 1 liter to 5-10 square meters.
- Recommended layer thickness 100-200 microns wet.
- Dry layer thickness is recommended – 60-120 microns.
- Flexibility – 1 mm (sheen) Density – 1.1-1.3 gm\cm3
- Average viscosity A+B in matte shine – 115 krebs
- glossy color viscosity B+A – 95 krebs
- rigid– 10< Dg (Ericsson)
- Abrasion – 120 microns – 3600 cycles (Gardner) ASTM with fiber – 4800 cycles
- Basic to hardened ratio – 2:1 or 4:1
- Packed paint durability time – 6 hours (viscosity growth no more than 6 seconds original viscosity)
- milling size – glossy 7 > Hagman, Matte 5 > Haggman
- Gloss at 60o – Glossy 80% <, silk 15-45%, matte %3 > 60 degree lens and >8% in lens 85 degrees.
Polyurethane polyester with fiberglass fibers
- Permitted hue changes – Delta E – 1.0 >
- Pot Life = Working time from the moment of mixing B+A – 6 > hours.
- Resistance to distilled water 24 hours – without loss of adhesion or corrosion an hour after extraction from the liquid.
- Carbon resistance – without loss of adhesion an hour after extraction from the liquid.
- Resistance to acids – 24 microns of dry film dipped 1 hour in the solution at a concentration of 10% acetic acid – without any damage to the integrity of the film or change in the hue.
- In oil 1250 24 hours in OC 121- without loss of adehyde 4 hours after extraction from the liquid.
- Resistance to hydraulic oil24 hours in OC 66 – Without loss of adhesion 4 hours after extraction from the jet fuel resistant liquid – 7 days at temperature room – without loss of adhesion 4 hours after the heat resistance fluid is removed – O C121 for 60 minutes. No hue changes to Delta E=1.
- Humidity cell – 300 hours in humidity 100% in OC49 temperature without loss of adhesion or damage to film an hour after extraction from the salt cell liquid – without the appearance of corrosion.
- Thermal shock – no adhesion losses.
- Paint removal – up to 90% will be removed by immersion in a color remover for 60 minutes.
- Solids % –65% solid..
Denbergloss Polyester HD – polyurethane polyester Armored
Polyurethane polyester with fiberglass fibers
Contains:
- Polyol Polyester suitable for resistant to chemicals and durable pigments.
- Special materials.
- Solvents, additives.
- In part 2 of the keys – UV-resistant aliphatic Isocyantes, a special composition with a catalyst.
- Fiber separately as part of C
Shade:
- All Shades of RAL
Gloss:
- Matte Standard.
- glossy,
- silk on order.
Drying to the touch:
- 30 minutes.
Drying between layers: for an additional layer -30 minutes, hard drying – 3 hours, final drying – 4 hours.
Application methods:
- brushing, scrolling, splashing
Dilution:
- 10-35% Thinner 11 – D pressure 3-4 atm.
- Brushing/rolling – can be diluted or up to 20% in diluted 11 – D if smear bars or “orange peel” are formed during application.
- In summer, slowing down drying if OVER SPRAY is created, it is recommended to add a retarder.
Preparation of surface:
- thorough cleaning dust, fat, dirt and loose color.
- Rub with glass paper to remove grains and air pressure owls.
- Filling large holes and sockets with polyester sewage.
- New primer or primer fixes with “Epoxyden Ship Primer”
Denbergloss Polyester HD – polyurethane polyester Armored
Polyurethane polyester with fiberglass fibers
Primer coat:
- Epoxyden Ship Primer.
Packaging:
- 3.4+1.6 = 5 liters.
Storage:
- In a cool, shady place at room temperature.
- Keep lids tightly closed.
Shelf life:
- 12 months in the original packaging.
Tools Cleaning:
- 11-D thinner at the end of painting.
Safety:
- Not edible, out of reach of children.
- Flammable, away from heats, fire and sparks. Smoking is not allowed while on work.
- Ensure proper ventilation during application. Air must be provided if necessary.
- Wear goggles, solidarity gloves, protective clothing.
- In case of injury , seek medical attention immediately.
- Be sure to carefully read safety instructions on the label
Warning:
- Do not mix with materials not recommended by us.
- Avoid contact with the skin and eyes, causing dryness and irritation of the skin.
- In contact, rinse with plenty of running water and seek medical attention.
Quality audit:
- In our factory laboratories in accordance with MIL-C-PRF 85285C specifications and MMS-420 specifications. also
- ISO 9001-2015. also
Denbergloss Polyester HD – polyurethane polyester Armored
Polyurethane polyester with fiberglass fibers
User’s Attention:
- This technical specification is for general non-binding information only. The product is a professional product for professionals only who have already acquired previous experience in its implementation. This specification does not serve as a substitute for advice/training by an authorized consultant/guide. It is mandatory to apply to a small area for match testing first before applying large areas. The content of this specification changes over time and updates are entered, and updated versions must be requested. Names of consultants/professional instructors can be obtained by telephone. Instructions should be read in… also
- Manufactured by Denver Colors & Coatings Israel Ltd., 80100 Sderot, 80100, certified by the Standards Institution of Israel in accordance with ISO 9001-2015 standards. also
Denbergloss Polyester HD – polyurethane polyester Armored
Polyurethane polyester with fiberglass fibers
- For more information about Denber Paints and Denber Projects, please contact us by phone and/or to the company’s websites:
- company profile English also
- For more details please refer to the Denber website also
- For our Facebook page click here also
- To the Facebook page of the CEO of Denber also
- For more projects click here also
- To the article: Sealer for stone and concrete and marble also
- To the article: Thermal insulation in nanotechnology also
- article: Thermal insulation Thermosil 200 energy saving in green construction also
- Related article: Thermal insulation, floor coating also
- To the article: Thermal insulation in nanotechnology company Denber also
- Fire resistance of houses, hardwood and parquet floors, decks also
- Swelling paints for steel protection against fire – Fire retardant paint also
- Epoxy floor coating in casting and painting also
- Crystal epoxy resin for tables also
- To the article Sealing also
- The complete article on the sealing materials for roofs and walls also
- Sealing the floor of the balcony, terrace from rain also
- Mold, how to remove mold correctly and how to fight mold also
- “Sick” buildings – Antibacterial paints Bacterinoll/ Tutgum Bacterinol also
- Paint for aircraft Denbergloss Jets also
- Asphaltflex execution specification – Denber Paints also
- Denbergloss grainy car paint also
- Denbergloss Clear also
- Varnish for wood. How to choose the right varnish for wood also
- Crystal epoxy for tables from Denber also
- Paint for swimming pools, epoxy Epoxyden Dengal, performance specification also
- Color specification of quadrant helmets also
- For a free consultation, call Denber – Dr. Blen Evgenia – 050-3551549 / 050-3551551 also
- Need advice? Contact us by email: Denber@bezeqint.net or contact us at 08-9960794
Polyester HD – polyurethane polyester Armored
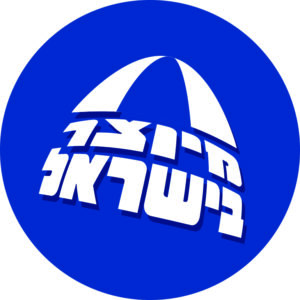
Denbergloss Polyester HD – polyurethane polyester Armored. www.denber-paints.co.il