Polyplex radon gas sealing
Two-component sealant coating prevents 100% gas passage
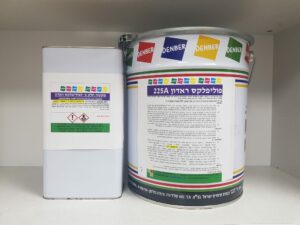
Polyplex radon gas sealing www.denber-paints.co.il
Advanced Gas Isolation Coating Solvent free coat against radon gas penetration.
Radon Gas Barrier: Professional-Grade Polyurea Coating System (1:3 Ratio)
Our 100% solids two-component Polyurea coating system delivers superior radon gas isolation for wall applications. This specialized formulation creates an impermeable barrier that effectively blocks radon gas migration through structural surfaces.
Technical Specifications: This high-performance dual-component Polyurea coating is engineered for extreme conditions, featuring enhanced chemical cross-linking that significantly outperforms conventional polyurethane systems. The polyol-isocyanate chemistry creates a dense molecular network that prevents gas molecule penetration at the microscopic level.
Applications: Specifically designed for environments requiring gas containment, this system provides exceptional sealing properties for infrastructure exposed to gas emissions. The coating’s molecular structure creates a complete barrier against radon and other gas permeation.
Two-component sealant coating prevents 100% gas passage
Performance Characteristics:
- Exceptional abrasion resistance.
- Superior chemical resistance.
- Extreme load-bearing capacity.
The versatile application methods include direct casting for gas storage vessels, utilizing rotational techniques to ensure uniform coverage and maximum hardness. The system can be applied at 300 microns thickness using standard methods including brushing, rolling, or spray application.
It passed tests at the PROTON Institute. Test report No. RPT-2116 attached
Technical Properties:
- Composition: 100% solids, solvent-free formulation.
- Chemical Resistance: Superior durability against acids, alkalis, oils, greases, cleaning agents, and diverse industrial chemicals.
- Gas Barrier Performance: Exceptionally dense molecular structure prevents gas and air molecule permeation.
- Mechanical Properties: Highly resistant to impact damage, surface abrasion, and heavy load compression.
- Underground Application: Ideal for subterranean shelter walls, providing protection against gas infiltration and groundwater penetration.
- Surface Finish: Creates uniform, seamless, smooth coating.
- Adhesion: Excellent bonding capability with compatible primers (Denbertex primer/Epoxyden aqua primer) for cementitious, concrete, and gypsum substrates.
- Hardness Profile: High mechanical hardness with exceptional wear resistance.
- Thermal Stability: Withstands dry heat exposure up to 200°C for short durations and 100°C for extended periods.
- Installation Flexibility: Solvent-free composition allows application in limited ventilation environments.
- Elasticity: Exceptional flexibility with complete shape recovery without deformation.
- Electrical Properties: High electrical insulation capability.
- UV Response: May exhibit yellowing with prolonged sun exposure without compromising performance characteristics.
Two-component sealant coating prevents 100% gas passage
Primary Applications:
- Radon Mitigation: Specialized coating for underground structures to prevent radon gas infiltration.
- Gas Containment: Interior and exterior protective lining for gas storage vessels.
- Pipeline Protection: Protective coating for pipes and containers storing gases or low-boiling-point solvent emissions.
- Asphalt Surface Treatment: Sealing layer for asphalt surfaces vulnerable to underground gas permeation.
- Critical Infrastructure: Containment coating for nuclear facilities to prevent gas leakage.
Technical Specifications:
Coverage Rates:
- Standard Thickness: 100 microns = 1 liter/10 m²
- Recommended Application: 330 microns = 1 liter/3 m²
- Application Note: For vertical walls, apply three 100-micron layers to prevent material migration and ensure optimal sealing
Physical Properties:
- Density:
- Part A (Grey RAL7032): 1.3 g/cm³ (DIN 51575)
- Part B (Clear): 1.0-1.1 g/cm³
- Mixing Ratio:
- By Weight: 18.5 kg : 5.2 kg = 23.7 kg (A+B)
- By Volume: 3:1 (A+B)
- Solids Content: 100%
- Flash Point:
- Part A: 255°C (DIN 53213)
- Part B: 166°C (DIN 53213)
Two-component sealant coating prevents 100% gas passage
Performance Characteristics:
- Hardness: >Dg 3 (ERICSON), >60 (DIN 53153)
- Flexibility: 1 mm at 120 microns film thickness (SHEEN)
- Elongation: 50-150%
- Viscosity:
- Part A: 5,000-15,000 cPs at 25°C (Brookfield)
- Part B: 85-100 cPs
- Mixed A+B: 2,200 cPs average
- Abrasion Resistance: 40 mg weight loss per ASTM 4060 (CS-17 wheel, 1 kg load, 4,500 cycles)
- Adhesion:
- To Concrete: Exceeds substrate strength
- To Epoxyden Floor Primer: 245 kg/cm
- Tensile Properties:
- Flexibility in Drag: 10% N/mm² (DIN 53457)
- Drag Resistance: 8 N/mm² (DIN 53455)
- Electrical Insulation:
- Standard: 15×10¹³ ohm/cm
- Transparent Version: 1.5×10¹⁴ ohm/cm³
- Structural Strength:
- Bending Strength: 40-60 N/mm²
- Pressure Strength: 800 kg/m²
- Stress Strength: 600 kg/m²
Application Parameters:
- Working Time (pot life): 60 minutes at 20°C
- Cure Times:
- Minimum Before Use: 24 hours
- Final Cure: 3-7 days
- Chemical Exposure Readiness: 7 days
- Application Conditions:
- Temperature Range: 5°C-32°C
- Maximum Relative Humidity: 75%
Two-component sealant coating prevents 100% gas passage
Composition
- Advanced Polyurea resin system
- Specialized hardening agents
- High-performance structural fillers
- Industrial-grade pigments
- Reinforcing fibers
- Performance-enhancing additives
Aesthetic Properties
- Standard Color: Grey
- Color Options: Available in full RAL color range
- Finish: Silky sheen
Curing Profile
- Touch Dry: 2-4 hours at 25°C (330 microns thickness)
Temperature-Dependent Curing Schedule
For 500 microns layer thickness:
Temperature | Initial Cure | Final Cure |
7°C | 6 hours | 5 days |
10°C | 5 hours | 4 days |
15°C | 4 hours | 3 days |
20°C | 3 hours | 2 days |
30°C | 3 hours | 2 days |
40°C | 2 hours | 1 day |
Recoat Intervals
- Minimum Recoat Time: 12-16 hours
- Maximum Recoat Time: 16-24 hours
- Complete System Cure: 3-7 days (temperature dependent)
Two-component sealant coating prevents 100% gas passage
Ventilation:
- Does not contain any solvents so that a medium amount of air is required.
Application methods:
- Pour \ spread or spray with airless (high pressure ratio) for thin coating.
Thinning:
- No thinning needed. To coat small areas, it is required to make a suitable amount of mixture for immediate use.
- For spraying with spray gun or low pressure airless, – reduce viscosity as needed with thinner D- 11 or thinner XL.
Surface preparations:
- Concrete: apply on absolutely clean surfaces. Spread Epoxyden floor primer (see product application) in case the concrete absorbed the primer leaving crumbs applies another layer of primer floor.
- Natural stones: clean with a lot of water in high pressure and dry completely.
- Asphalt: clean thoroughly with high water pressure in order to get an absolutely clean surface. Wait until the surface completely dries.
- Aluminum: apply a layer of Epoxyden Strontium chromate/Epoxyden wash primer (see instructions for the product)
- Steel: apply a layer of Epoxyden 19.
Two-component sealant coating prevents 100% gas passage
Instructions:
- Make sure that the base/primer layer is dry, clean; dirt, dust and grease free.
- Floor – Open carefully ‘A’ +’B’ sections of the Polyflex 225A and pour at the ratio 3:1 the required amount according to the volume = surface calculation for double layer coating.
- Stir the mixture well with a slow mixer and immediately pour on the surface. With a large wiper spread the mixture evenly on the entire surface. For large surfaces a portable cement mixer could be used in order to make over 200 liters at once in case that the material could be spread on the entire surface within 30 minutes, so it won’t harden and it won’t be possible to pout it while it is still liquid on the surface.
- Wall – prepare small quantity a+b ratio: 3:1 and spread with an epoxy roller a thin approx. 100 mics. First layer. After 16-24 hr. spread the second layer. After another 16-24 hr. spread the third layer.
- Same can be done with hydraulic airless after diluting with thinner D-11 10-35% to achieve the required viscosity.
Two-component sealant coating prevents 100% gas passage
Packaging:
- 4.5+13.5=18 liters.
Storage:
- Store in a shaded place, at a temperature of between 15°C-32°C.
Shelf-life span:
- 24 months in its original package. The hardener (part b). if storage not as required – 12 months
Equipment cleaning:
- Use D-11 thinner immediately after applying.
Quality control:
- In factory laboratories according to specifications. also
- COA and COC certificate. also
- ISO 9001-2015
Safety precautions:
- Inedible, keep away from the reach of children. also
- While applying, good air ventilation is important. In case there is not enough air, use ventilation according to the ventilation table. also
- Wear protective glasses, gloves and suits. also
- Avoid direct contact of the paint and/or thinner with the eyes and skin. In case of contact, immediately wash thoroughly with water. also
- In case of an injury immediately get doctors assistance. also
- Read the safety instructions on the labels. also
- See M.S.D.S
See also one-component radon polyflex for sealing against radon gas
For the full specification: radon polyflex radon gas sealing
Two-component sealant coating prevents 100% gas passage
- For more information about Denber Paints and Denber Projects, please contact us by phone and/or to the company’s websites:
- company profile English also
- For more details please refer to the Denber website also
- For our Facebook page click here also
- To the Facebook page of the CEO of Denber also
- For more projects click here also
- To the article: Sealer for stone and concrete and marble also
- To the article: Thermal insulation in nanotechnology also
- Related article: Thermal insulation Thermosil 200 energy saving in green construction also
- Related article: Thermal insulation, floor coating also
- To the article: Thermal insulation in nanotechnology company Denber also
- For a free consultation, call Denber VP Dr. Blen Evgenia – 050-3551549 / 050-3551551 also
- To the article Sealing also
- Epoxy floor coating in casting and painting also
- The complete article on the sealing materials for roofs and walls also
- Asphaltflex execution specification – Denber Paints also
- Denbergloss grainy car paint also
- Lampert Denbergloss Clear also
- Crystal epoxy for tables from Denber also
- Paint for swimming pools, epoxy Epoxyden Dengal, performance specification also
- Color specification of quadrant helmets also
- Need advice? Contact us by email: Denber@bezeqint.net or contact us at 08-9960794 also