Specifications for concrete floor polishing
Specifications for concrete floor polishing
Sealers for sealing concrete floor polishing and sealing with sealers
The goal:
- Treatment of cast concrete after curing, to obtain an opaque concrete surface protected from water and dirt penetration, with a natural or semi-transparent appearance for blurring and filling stains and cracks, glossy or matte, with a natural or varied transparent appearance for RAL 7044 or RAL 7040 gray concrete color
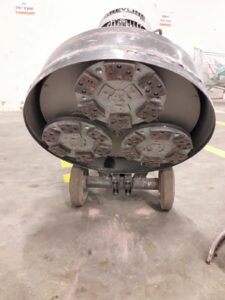
- New helicopter smoothed concrete – removing all dirt and dust, vacuuming the surface and preparing for polishing.
- If there is some light grease on the concrete and the grease has not penetrated the concrete (oil leaks from vehicles, dripping oil drops, applied grease, etc.) – dissolve with ” ZX -12 degreaser” by rubbing (road sweeper or machine) and washing with water, after drying – start polishing.
- If there is fat penetration deep into the concrete (a large spill of thin oil on concrete without a suitable sealer or protective epoxy coating and deep penetration) – spreading an emulsifier ” to the oil” N “to absorb the fat” and washing with water until foam stops coming out. After drying – start polishing. Deep polishing to the depth of oil penetration will be required.
- If there is a layer of grease/hardened soot (layers upon layers of oils and lubricants that have dried and hardened and formed a layer of hardened soot on top of the concrete) – spreading ” Carbon Cleaner ” (beware of a dangerous and aggressive substance – full protective clothing and a suitable breathing filter) allowing soaking time for softening and rubbing until complete melting/softening and mechanical scraping until obtaining concrete free from oil/hardened soot, dispersion into N oil and washing with water to remove residual dissolved oil. After drying – start polishing. A very deep polishing will be required until you get a white and clean concrete.
Sealers for sealing concrete floor polishing and sealing with sealers
Polishing:
- First step – coarse and deep polishing – diamond polishing with a double helicopter machine with 6 diamond discs or a large diamond disc “7-“9 for small areas. During polishing, the machine must be connected to a vacuum system, and the polishing worker must wear protective glasses and a dust mask. A layer must be removed according to the condition of the concrete until all grease stains and/or concrete juices are removed in new concrete (stains that are formed from the rise of concrete juices after smoothing the surface with a helicopter)
- For a smoothed concrete surface with only stains of concrete juices, there may be no need for a first stage of diamond polishing which may add unnecessarily deep scratches, you should first check polishing with stones or 24 or 30 glass paper and if the concrete juices are well removed there is no need for diamond polishing (first stage).
- Second step – after polishing a first step diamond or coarse paper, vacuum well, and change to paper or 120 grain stones, polish well and vacuum.
- And the third step – change to core 400 and repeat the operation.
- And the fourth step – change to grain 800 for a matte finish, or grain 1500 for a silky finish or grain 3000 for a glossy finish.
Sealers for sealing concrete floor polishing and sealing with sealers
Sealing – sealers:
1. Option A – water-based transparent acrylic sealer 16 . Apply with a mop or roller or spray for full coverage. It is recommended to repeat the operation once more for full filling and impregnation of the concrete. Do not leave puddles of the sealer.
2. Option B – sealer Xk-90 water-based transparent polyurethane. Apply with a mop or roller or spray for full coverage. It is recommended to repeat the operation once more for full filling and impregnation of the concrete. Do not leave puddles.
3. And also option C – siloxane 290 sealer , polysiloxane diluted with turpentine. Apply with a mop or roller or spray for full coverage. It is recommended to repeat the operation once more for full filling and impregnation of the concrete.
4. And option D – transparent epoxy fluor sealer, a two-component transparent epoxy sealer that penetrates deeply into concrete floors that are not exposed to the sun . Apply with a mop or roller or spray for full coverage. It is recommended to repeat the operation once more for full filling and impregnation of the concrete.
5. Option 5 – Danberglus clear clear sealer, a very strong two-component penetrating elliptical polyurethane sealer, abrasion resistant, UV resistant for concrete floors exposed to the sun . Apply with a mop or roller or spray for full coverage. It is recommended to repeat the operation once more for full filling and impregnation of the concrete.
6. Option 6 – Dunbargloss sealer, semi-transparent variety in RAL 7044 concrete shade or RAL 7040 gray shade. A very strong two-component penetrating elliptical polyurethane sealer, abrasion resistant, UV resistant for concrete floors exposed to the sun . A variety for blurring stains and capillary cracks and for obtaining a concrete surface with a uniform tone. Apply with a mop or roller or spray for full coverage. It is recommended to repeat the operation once more for full filling and impregnation of the concrete.
Sealers for sealing concrete floor polishing and sealing with sealers
Note: to hide and fill capillary cracks up to 0.5 mm in concrete before applying sealer, you must prepare a variety of Dunbargloss sealer mixture in concrete shade 7044 or gray 7040 with the addition of Cabosil powder for certification until a thick colored paste is obtained and fill cracks in concrete with a putty. After complete drying, you can go over again on the same places until you get a filling to the height of “zero”. After drying, you can apply the various sealer with a roller or by spraying to obtain a uniform surface without signs of dirt, whiteness, differences in the tone of the concrete or cracks.
For larger cracks – from 0.5 mm and above, use a flexible or hard epoxy putty for small cracks.