Specification for restoration of concrete
Specification for restoration of concrete
And this specification comes to define the method for restoring and restoring concrete while creating cathodic protection (cold galvanization) for the cast iron and barrier protection to prevent moisture from entering the cast iron and accelerating its rusting.
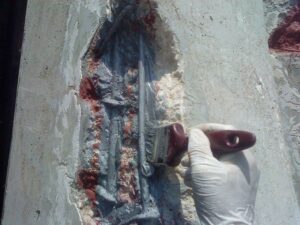
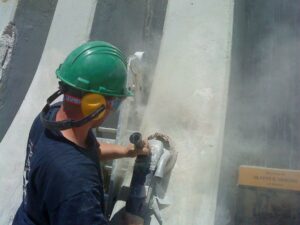
A method for restoration without the use of cement products to extend durability for at least a decade.
Restoration and restoration of concrete for decades of durability with epoxy and polyurethane
Preparation of the area :
- Chipping, cutting and removing loose and cracked concrete parts until a clean and stable concrete surface is obtained.
- Exposing the iron in its entire circumference, and at least about 1 cm behind it, and about another 5-10 cm on both sides of the rusty/damaged iron until you get a stable iron free from corrosion damage.
- Sharpening disc or steel brushes until you get white iron free from rust, as well as sharpening rust stains in concrete until you get clean concrete.
- Washing with water under pressure to remove dust and dirt and drying with wiping and natural.
Protective treatment for sperm iron:
- Painting the steel and concrete with an anticorrosive primer epoxy primer layer that converts rust in a layer of about 50 dry microns. Drying 2-4 hours up to 24 hours.
- Do not paint about 1 cm of the steel at the entrance to the clean concrete.
- Applying a layer of zinc-rich epoxy to the entire feed iron including the 1 cm gap left to create cathodic protection. Drying 24 hours. Minimum thickness 250 microns dry.
- Painting a layer of epoxy sulcot aluminum for membrane protection with a thickness of at least 150 dry microns.
Concrete restoration:
- In order to avoid waiting for curing, the concrete must be restored by applying epoxy putty to obtain the original shape or pour into a mold or pour grout to the floor up to zero height.
Specification for restoration and restoration of concrete
Restoration and restoration of concrete for decades of durability with epoxy and polyurethane
Technical specifications for the restoration and restoration of concrete and the sealing of electrical cable crossings on the road
Purpose: This specification comes to define the method for restoration and restoration, sealing and protective coating for concrete surfaces in electrical cable crossings on the road to prevent water infiltration and a coating that is durable and suitable for vehicle travel.
Preparation of the area :
- Complete vacuum diamond polishing of all concrete areas including polishing the joints of the concrete panels, until obtaining white and clean concrete without any contaminants or bitumen residues. Concrete protrusions above zero height must be polished up to 3 mm below zero height.
- Thorough vacuuming of the entire area and the seam connections between the concrete slabs.
- Do not work on damp or wet infrastructure, it is mandatory to work on hot days and hours after the morning dew has dried.
Primer:
- Apply a transparent penetrating epoxy flour primer (1:1 ratio of base to hardener) until saturation without leaving puddles, on all polished concrete surfaces and seam joints. 6-24 hours drying and applying another thin layer.
Restoration and restoration of concrete for decades of durability with epoxy and polyurethane
Flexible filling for seams/concrete joints:
- For deep recesses: preparing a mixture of Polyplex 225 (3:1 ratio of base to hardener) with quartz sand until a thick mixture and filling the deep recesses up to 3 cm from zero height. Waiting for drying 6-24 hours.
- Preparation of the polyplex 225 mixture (3:1 ratio of base to hardener) and filling the sockets of the concrete joints up to zero height minus 3 mm. Waiting for drying 6-24 hours.
Molded coating up to zero height:
- Preparation of a 100% solids Dunbargloss Flor polyurethane mixture, black shade (2:1 ratio of base to hardener) You can add 1/3 of the quartz mixture and pour on the surface up to zero height, level and go over with a spiked roller to remove bubbles. Waiting for drying 24 hours.
- Do not pour from the bucket in which the mixing is done, transfer to another vessel and mix again and then pour. This is because this material does not mix by itself and remains unmixed material with the hardener on the sides and bottom whose casting on the surface will never dry.
UV protection coating :
- Coating with a protective layer of Danberglus Fluor paint in a black shade (2:1 ratio of base to hardener) applied with a roller or airless spray. 1 liter per 5 square meters. Drying 24 hours. Apply or spray another layer.